Smart Manufacturing
The past 50 years in the automotive BiW industry have given us an enormous amount of experience on how to automate production processes and also what not to automate. During these years, we have developed a process and function library that holds a vast quantity of sub processes that can be used for specific production lines. With this approach, we are able to build customised solutions using already present function blocks such as robot handling, bin picking, AGV/AMR solutions and a large quantity of joining technologies.
At the heart of each manufacturing solution weather it is fully automated, manual or hybrid is the control system. It manages and optimizes the equipment and resources of a manufacturing proces to ensure efficiency, consistency and a qualitive output. At VDL Steelweld we have developed an ready to use standard that enables our customers to tap into our 5 decades of automation experience.
The world of Smart manufacturing is very broad and can include various automation requests; the below image shows some highlights of the competences at VDL Steelweld.


Machine Tending
Automating the handling of parts from and to machines has several benefits such as; enhanced productivity, increased precision, increased consistency.
By delegating simple and repetative tasks to machines or robots, operators can focus on more complex tasks thereby boosting the overall efficiency of your manufacturing setup. Which is visible in reduced downtime and increased throughput figures.
Ultimately, automating machine tending not only elevates productivity but also drives innovation and profitability in a modern manufacturing environment.

Measurement Systems
Increasing the frequency and method of measuring by engaging in inline measurements increases your line of sight on product quality and efficiency.
Real-time data acquisition allows for quick adjustments, ensuring adherence to strict quality standards and minimizing defects. Enhanced accuracy and consistency in measurements guarantee uniformity across production batches, bolstering customer satisfaction and reputation.
With automated measurements seamlessly integrated into the manufacturing process, operational efficiency skyrockets, reducing waste and maximizing resource utilization.

Bin Picking and Part handling
Through advancements and innovations in sensor technologies the field of automation becomes broader and broader. Using smart sensory, products can be detected, scanned and/or measured. With this data automated systems can accurately locate, grasp and transport parts, components and products of different sizes and materials.
Part handling automation reduces labor costs, minimizes errors, increases troughput and improves visibility of logistic flows. with faster order fullfillment and reduced manual handling, customer demands can be met promptly while optimizing resource utilization.


Automated Warehousing
Warehouse automation revolutionizes logistics, enhances efficiency and accuracy while reducing costs. The combination of an automated warehousing system and a production line can be of great value. The direct coupling of inventory management to the requirements of your production line ensures a swiftly and timely delivery of parts and increases visibility on inventory, capacity and buffer sizes.


Process Control Systems
In the dynamic landscape of mordern manufacturing, precision and control are one of the drives for an efficient operation. With synchronized processes waste is minimized and productivity is maximized. By a solid and clean presentation of information to operators and/or controllers errors or inefficiencies are detected quickly and can be responded upon swiftly.
Through the correct level of process control efficiency isn't a goal it is a guarantee.

Quality Control
In a complex production environment sensors are your information gatherers. A solid quality control plan will enable the correct meausurent of all the paramaters at the necessary product phases throughout the production process. Armed with this data fluctuations are detected in real-time and anomalies are intercepted before they interve the production process.


Collaboration between Robot and Operator
In most cases the product characteristics and assembly sequence guides towards a certain manufacturing process. Depending on the variance between product types and volumes. More automated solutions or a more hybrid solutions can be choosen.
The manufacturing setup can be developed as future proof by having different setups as the product goes through its life cycles. Scalable or modular production lines are a good example of how a dynamic manufacturing setups could look like.

Robots and Handling Systems
Depeding on the requirements and or joining technologies used a wide variety of robots or pick and place units can be selected.
Equipping them with the necessary sensory and/or imaging function will enable a more dynamic approach towards process and product variances and will lower the bar on when automation makes sense. In todays automated production lines intelligent robots determine themselves which actions can be performared and evalute the correctes of the product in front of them before initiating the assembly step.


Automation with Robots
A robot is a very diversible tool when it comes to automation purposes. A wide variety of tools can be added such as, but not limited to: bolting, welding, riviting, glueing, handling/positioning, nailing, pressing, measuring, imaging, etc. With these options the automation potential is endless.
Finding the right automation fit with the product and its volumes is what we do best at VDL Steelweld.

Transport Solutions
Multiple options to move parts from A to B are possible. Standard or rigid solutions represent conveying systems that are route defined, more flexible solutions could be incorporated using AGVs. This type of logistics solution is escpecially valuable when setups might change over time as is the case with scalable or modulair manufacturing concepts.

The innovations in component technologies resulting in smart sensors, IIoT technologies, advanced imaging methods etc. makes it possible to build more advanced production systems which can handle more volume, more variance and higher quality levels then ever before. This opens up a whole new field in which automated production lines can be applicable. At the same time, the developed production lines become more complex in terms of operations, maintenance and control. At Steelweld, we make it our goal to design complex systems with an easy-to-use interface, enabling our customers to obtain the benefits of industry 4.0 manufacturing without experiencing the additional complexity.
For us, industry 4.0 does not equal automation; the operator has a skillset that cannot easily be replaced. The perfect mix between automation and operator involvement is achieved by following the characteristics of the product to determine the most effective and efficient way of manufacturing. The collaboration between robot and operator with industry 4.0 technologies can take your manufacturing activities to the next level.
The software that controls, monitors and steers the production line is the backbone of your production facility. To keep all the introduced complexity in controls VDL Steelweld has introduced the Smart Manufacturing Standard.
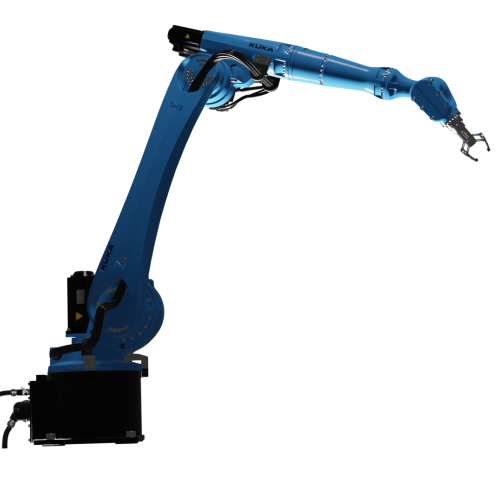
What we deliver
- Manufacturing enabling
Product evaluation in regards to the intended manufacturing process - Production process definition
Developing the manufacturing blueprint that leads up to a finished product according to the requirements and quality standards - Production line design and build
Define, design and build all the necessary equipment - Realisation
Install and commission the production line at your facility or at one of VDL Steelweld's facilities - Ramp-up and aftercare
Ramp-up the production volume to the volume target according to quality and output requirements